|
Brian’s Other Transportation
Related Projects
– In the little free time I have when I’m not maintaining this website,
working for BHRA or teaching classes (my other slightly better paying
job), I am often engaged in time-sucking projects like you
see below.
Other
Related projects –
Creative Engine Removal
– Fast
Glow Plug Diesel Conversion – Biofuel Conversion – Converting
a Diesel engine
to run off Used Vegetable Oil (Veg Fuel Benz #1)
– Diesel Motor Rebuild and Automatic to Manual Transmission Swap (Veg
Fuel Benz #2)
|
|
|
|
|
|
|
|
|
|
|
|
|
|
|
|
|
|
|
|
|
|
|
|
|
|
|
Creative
Engine RemovalAlternative method for removing
an engine from a vehicle.
Sawzall
(reciprocating saw), rescue saw blades, tow strap, front end loader
Note: I purchased
both cars for $500 and needed get
the engine outta the rusted out one into the red car, and therefore
create one working 4wd car. |
|
|
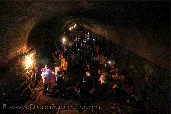 |
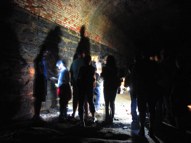 |
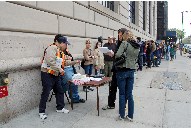 |
|
|
|
|
|
My 1989
Subaru – mint condition except for a blown engine- Shown being towed
from my friends farm where it was stored. |
A 1991
Subaru, horrible shape, but with a good engine – this is the donor car |
Step 1: cut
off the bumper, remove bolts that connect engine to transmission |
|
|
|
|
|
|
|
|
|
|
I did not have an engine
lift or a garage to work in, so
I had to think of an alternative means of accomplishing this task,
using unconventional methods. With the assistance of my
friend Travis
(who is an experienced heavy-equipment operator), we quickly and easily
accomplished this project. We used a Sawzall to cut off the
front of
the automobile, and a front end loader to lift the engine out of the
vehicle. |
|
|
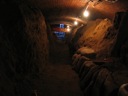 |
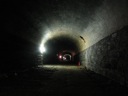 |
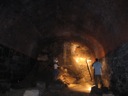 |
|
|
|
|
|
Step 2: cut
off the front of the car (including the radiator) |
Step 3: tie
tow strap around engine, remove engine mounting bolts |
Step 4: carry
engine to where you want it.
Step 5: Rip the rest of the parts you want off the donor car &
have it towed to the scrapyard. |
|
|
|
|
|
|
|
|
|
|
Fast Glow
Plug Diesel Conversion
Converting
the glow plug system from 1970s loop style (series wired) glow plugs to
modern (parallel wired) pen-type glow plugs. Converting the 1970s glow
plug controller to a modern glow plug controller.
5 pen
type German glow plugs, fast glow glow plug controller/relay, 70watt
fuse, electrical wire (8ga & 16ga), dielectric grease, crimp-on
wire connectors |
|
|
Unmodified Diesel Engine
|
Old Series-wire loop glow plugs
|
old type loop plug (top)
new pen-type plug (bottom) |
|
|
|
|
|
|
|
|
|
|
Note:
The installation of the fast glow system is a superior system for
warming the combustion chamber prior at start-up. The fast
glow system
is a slightly higher voltage system with more efficient modern
glow-plugs. This system allows the car to start in colder weather and
minimizes smoke at start-up. Also this system is designed to stay on
for up to 90 seconds during start up to improve engine performance,
reduce engine wear at startup and reduce emissions by insuring fuel is
burnt at a higher engine operating temperature. |
|
|
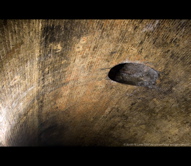
|
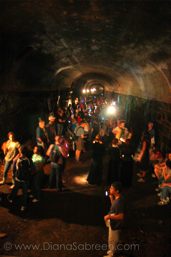 |
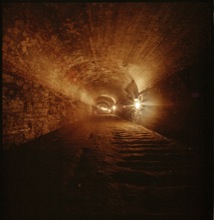 |
|
|
|
|
|
New
glow plugs installed, and each
plug tested for continuity |
New
parallel Glow Plug wiring |
The
new controller/relay (object with yellow dot on it) |
|
|
|
|
|
|
|
|
|
|
|
|
|
|
|
|
|
|
Diesel to
Biofuel ConversionConverting a diesel engine to
run off Used Waste Vegetable Oil (WVO)
Fuel
filter, fuel pump, alcohol safe fuel hose, polyurethane fuel hose,
marine-grade hose fittings, Teflon thread sealant, German
(unperforated) hose clamps , fuel temperature gauge, fuel temp.
sender/fitting, fuses, electrical relays, electrical switches, check
valve, on-off valve, 3/4″ coolant Tees, coolant hose, 12v filter heater
|
|
|
My 1976 MB 300 Diesel |
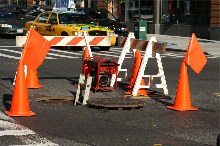
Unmodified MB 300 Diesel Engine |
Older diesel engines
will run well off of Vegetable
oil fuels if properly converted. The fuel system needs to be
modified when running vegetable oil. Since Veg Oil is more
viscous than diesel fuel the fuel must be heated up to 160-180 degrees
(F) to burn properly. 2 methods of adding heat are coolant
heat
and electric heat (I utilize both).
|
|
|
|
|
|
|
|
|
|
|
The
fuel systems on diesel engines supply the engine with more fuel than
the engine can use, in a conventional system this unused fuel is
returned to the tank. Most people running Veg oil install a
installing
a valve to loop your fuel, the fuel that has been warmed can be sent
back to the fuel filter (maintaining proper veg oil fuel temperature)
rather than back to the tank. |
|
|
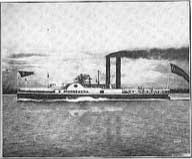 |
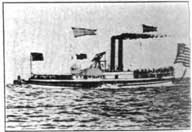
|
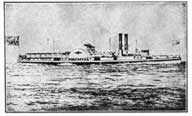 |
|
|
Many people feel that for
Mercedes diesel engines an additional fuel pump is not
necessary (if you use
a looped fuel system). However a lift pump of the right
psi will
improve performance and take the strain off your injection pump. |
|
|
The
three way (banjo) fitting (#1) on top of the fuel
filter is for the overflow (return) fuel. The default setup
is
for all the overflow to return to the tank (#2A).
Modifications:
3A – check valve to
insure one-way fuel flow.
2B – loop fuel line
3B
-valve to switch between a return to tank system and
an on-demand fuel system.
with this
system warm fuel is looped back into the fuel system and any air that
is trapped in the system can be returned to the tank (unlike a
conventional loop system). |
12V
Injection Line Heaters.
Heating elements wrapped in orange hi-temp silicone tape |
Here is the
new filtration system and boost pump I installed for running veg oil
fuel.
A – initial fuel filter with 60 micron cleanable stainless steel screen
(filters out the big chunks).
B- marine grade fuel pump
C- 5 micron fuel filter / water separator w/ coolant heat wrap and 12v
electric heater
D- electronics/fuses and relays for filter heater and fuel pump |
|
|
|
|
|
|
|
|
|
|
Fuel filtration must also be
improved – a water separating filter and a larger fuel filter (that is
heated) is ideal.
All
hoses used for fuel should be alcohol safe. Polyurethane,
Marine
grade or other fuel hose material approved for Ethanol/
Methanol.
All fittings and metal that
contacts fuel should ideally be made out of
non-reactive metal (marine grade plated steel, aluminum,
stainless). Bronze is better than brass, brass is better than
copper ( copper, galvanized and
iron/non-plated steel is usually avoided). |
|
|
 |
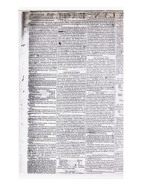 |
 |
|
|
|
|
|
Picture
of a Stanadyne brand water-separating Fuel Filter like the one I used –
these filters come in various lengths – use the longest one that will
fit in your vehicle (the bigger the filter the less frequently it will
need to be changed). Use a 5 or 10 micron filter
cartridge |
Home-made
coolant wrap – wrap 3/8″ fuel line (or other suitable hose) around your
fuel filter. This will serve as a heater for your fuel filter
|
To
supply the fuel filter wrap with warm coolant you need to tee into the
hose that goes from the engine block to the heater core(I installed a
shutoff valve here as well), Also, you will need to tee into the return
hose that goes from the heater core to the water pump. |
|
|
|
|
|
|
|
|
|
|
Diesel
Engine Rebuild and Auto Transmission to 5spd Conversion
This project takes a 1975 300D and a 1984 240D and combines the best
parts of both of them.
The
old skool styling of the Mercedes w115 body style (made from
1968-1976), the more powerful 5 cylinder 300d engine and the 5 speed
manual transmission (and all necessary components from the 240D).
Step 1 – tow the car back to NY |
|
|
My new 1975 300D – bought it in California, .
Although
It looks a lot like the veggie – Benz above, the orange Benz above now
is fixed up and sold (it has a new owner) and this tan Benz
with a
sunroof is my new project car – needs some work but the car is a
rust-free California car unlike anything you’ll find (at least for my
my $2000 budget) on the east coast |
Drove it home from CA (almost) – didn’t quite make it (transmission
went in Virginia)
|
|
|
|
|
|
|
|
|
|
|
|
Step 2 – Pull the engine and transmission |
|
|
|
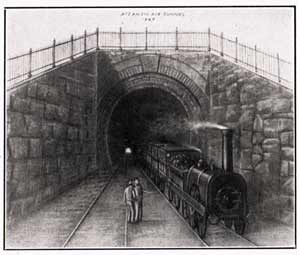 |
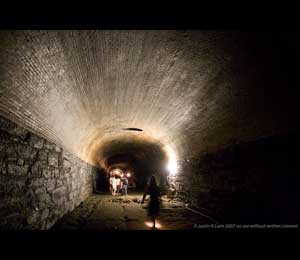 |
|
|
|
|
|
|
Brian & the
mysterious art of engine removal – it becomes less mysterious (and less
nauseating) when you turn off the truck that you’re lifting the engine
into. |
leaky engine, being hauled
off for the rebuild |
|
|
Step 3 – disassemble the engine and repair whatever
needs be be repaired inside the motor |
|
|
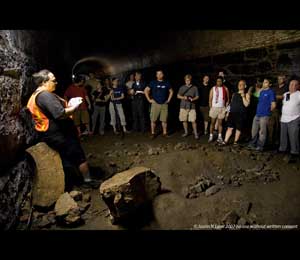 |
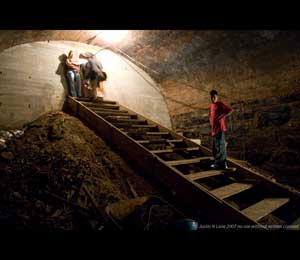 |
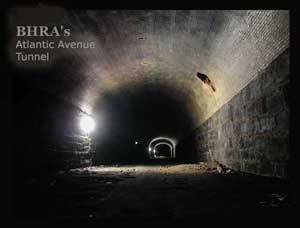 |
|
|
|
|
|
300D motor on stand w/ valve cover off |
300D motor on stand w/ cylinder head removed |
Strange yellow goop inside 2 cylinders |
|
|
|
|
|
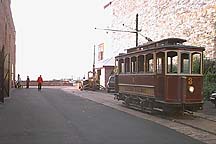 |
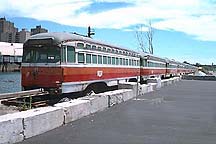 |
|
|
|
|
|
|
300D
motor with pistons out -3 of 5 cylinders had broken rings, bearings
were burnt so we decided to pull the crank and do a full rebuild
(instead of leaving the crank and main bearings in and just replacing
the rod bearings and rings) |
Crank, flywheel, harmonic balancer,
front crank pulley. All were brought to a machine shop where they were
cleaned, measured for tolerances, and balanced (only the crank itself
ended up being neutral balanced, everything else needed balancing) |
|
|
|
|
|
|
|
|
|
|
|
Step 4 – Pull transmission parts from the 240D
1984 Euro-Spec 240D
– The Doner Car before it was sacrificed
|
|
|
1984 Euro-Spec 240D
This is the doner car – rusted out body but it’s guts will live on |
1984 Euro-Spec 240D
|
1984 Euro-Spec 240D
|
|
|
Step
5 – put engine back together, put new adapter plate and 240D manual
flywheel on engine during reassembly, mate with 5 speed auto
transmission
|
|
|
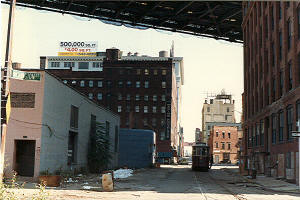 |
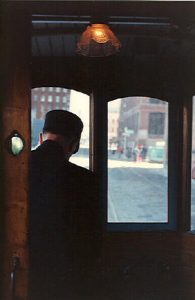 |
|
|
|
|
|
|
w115 300D engine mated with the 1984 Getrag 5 speed
In
1975 300D’s in America only came with automatic transmissions. Some of
the models sold in Europe may have been sold with 4spd standard
transmissions. However, 5 speed transmissions were not
available with
the diesel engines (240D or 300D) until 1984. |
The
rebuilt engine all back together: the vac pump was taken apart
and put together 90 deg off, but we modified the vac lines to make
it work
Also, make sure to replace all those old Phillips head
hose clamps, they wont tighten sufficiently and strip easily –
therefore coolant leaks everywhere and they are way more difficult to
change once you drop in the engine. |
|
|
|
Step 6 – install MT components, (pedals, shifter, etc) |
|
|
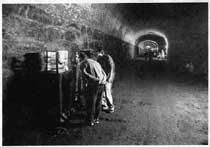 |
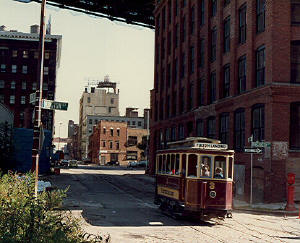 |
|
|
|
|
|
|
manual shifter installed (fit with little modification – just had to add 2 extra bolts) |
New
Drive shaft – I had to have this lengthened by 3in – Fleetpride in
Syracuse, welded a new piece of metric pipe to the solid parts on the
ends of the shaft, then balanced and painted it |
Shift
and brake pedal assembly fit, but pedals had to be bent considerably to
fit correctly (so the pedals are in the location they should be in.
|
|
|
Step 7 – drop in Engine and transmission |
|
|
|
|
|
|
|
|
|
|
|
|
|
|